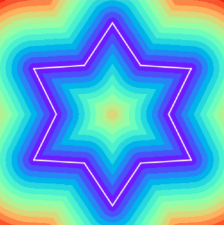
Minchen Li from the University of California, Los Angeles proposes solid and computational modeling focus on consistent principles for three-dimensional shapes within their study, Reliable Contact Simulation With IPC. With critical differences from other types of simulations like 3D modeling, solid modeling highlights physicality and ensures all surfaces meet correctly at points of contact. Points of contact are everywhere in everyday life, from driving to assembling furniture to physical phenomena like rain. Effectively modeling and predicting solids is vital to many other subdisciplines like computer graphics, mechanical engineering, and robotics.
For example, mechanical engineers deal with all things that move. They might use CAD systems to visualize different components in a part. To create that solid simulation, they have to be aware of points of contact. Especially for thin and deformable objects, it’s even more difficult to create models that accurately illustrate thickness and various points of contact. Imagine trying to create an accurate computational model of cards shuffling or a twisted tablecloth.
IPC for Complex Materials
Incremental potential contact (IPC) is a robust and efficient solution to build solid simulations with accurate contact geometry and dynamics. Using design sensitivity information, engineers can build thin, deformable solid objects with different spatial discretization. Traditional solid simulation methods lack the intricacy of IPC and leave engineers unable to create important dynamic details reliably. However, IPC offers reliable contact simulation with versatile materials, severe deformations, large time intervals, and more, making it a go-to solution for complex objects. In the future, more can be added to the IPC framework, like elastoplasticity, fracture mechanics, and solid-fluid coupling, to make it even more robust.
Download “Reliable Contact Simulation With IPC”